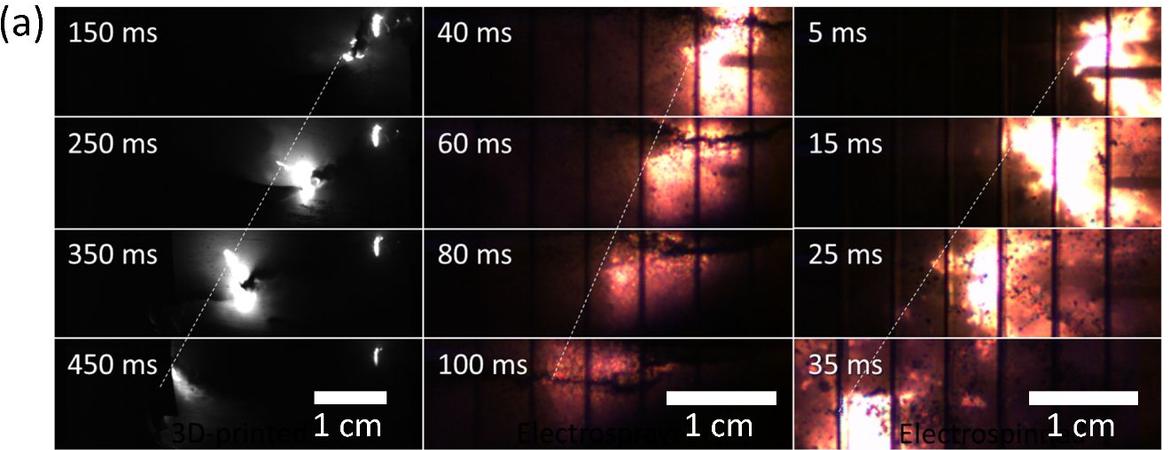
H. Wang, D.J. Kline, M. Rehwoldt, T. Wu, W. Zhao, X. Wang, & M.R. Zachariah. Architecture can significantly alter the energy release rate from nanocomposite energetics. ACS Appl. Polym. Mater. (2019). doi: 10.1021/acsapm.9b00016
With the advent of additive manufacturing methods combined with the increased interest
in using nanoparticle components to formulate energetics materials, structure-function
relationships and manufacturing methods have become intertwined. In this paper we
explore three different approaches to formulate composites and evaluate the combustion
properties. Here polyvinylidene fluoride (PVDF) was used to assemble both aluminum
nanoparticles (Al NPs) and ammonium perchlorate (AP). Three different fabrication
techniques: 3D-print, Electrospray (E-spray) and Electrospin (E-spin) were employed in
this work. Composites of Al/PVDF and composites with a high oxidizer content,
employing AP, were studied. The relationship between architecture and the burning rate of
both Al/PVDF and Al/AP/PVDF was investigated by studying the thermal decomposition
at high and low heating rates, and flame temperatures via color camera pyrometry on
micro-scale ignition/combustion events. By studying the release of HF, ignition
temperatures and the flame front, we propose a mechanism for combustion of the
multicomponent energetic films. Flame temperature, completeness of reaction and a
significant difference in ignition temperature appear to favor the E-spray material.
However, the large difference in propagation velocity between E-spray and E-spun, given
the minor difference in density clearly points to the importance of micro-architecture on
reaction properties. The relative energy release rate of E-spun Al/PVDF compared to the
E-sprayed and 3-D printed case is an enhancement of ~ 6X and 18X, respectively, and the
energy release rate of E-spun Al/AP/PVDF is ~19X higher than that of E-sprayed and 3Dprinted
samples. This implies that the lowest density spun material offer the highest mass
energy release rate by far.